Decarbonizing the Built Environment : A Definitive Guide to Carbon Zero Buildings
Under the 2016 Paris Agreement, 197 countries, including Thailand, agreed to reduce carbon emissions by 50% by 2030 and to zero by 2050, to avoid the worst impacts of climate change. The urgency to address climate change is becoming increasingly undeniable and the built environment plays a crucial role in this challenge.
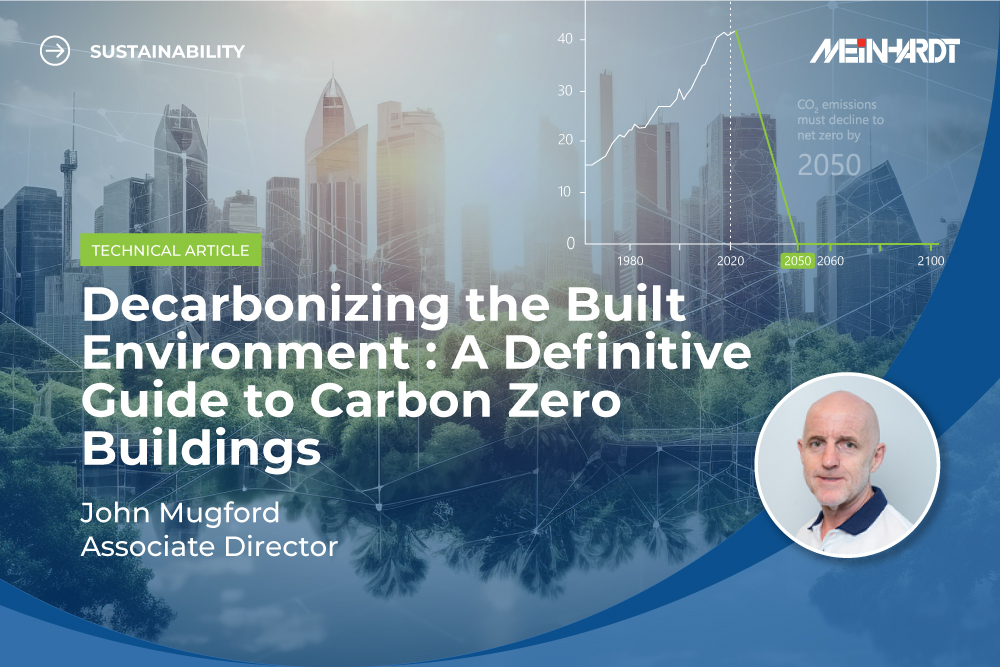
Under the 2016 Paris Agreement, 197 countries, including Thailand, agreed to reduce carbon emissions by 50% by 2030 and to zero by 2050, to avoid the worst impacts of climate change. The urgency to address climate change is becoming increasingly undeniable and the built environment plays a crucial role in this challenge.
Here in Thailand, Meinhardt are committed to partnering with the real estate industry to help achieve these ambitious sustainability goals.
This guide explores the concept of carbon-zero buildings and offers practical strategies and insights relevant to theses.
WHY ARE CARBON ZERO BUILDINGS IMPORTANT?
Buildings currently account for roughly 40% of total global greenhouse gas emissions and this number is increasing due to the global trend of rapid urbanization. The global building stock is expected to double by 2060, Globally, a New York City equivalent is expected to be constructed every month for the next 40 years.
It is therefore vital that the building sector focuses on decarbonising new buildings and improving existing buildings to achieve meaningful greenhouse gas emission reductions, as a critical step towards mitigating climate change and building a more sustainable future.
However, this is not just important due to climate change. Reducing a building’s carbon footprint is a win-win:
- Reducing operational carbon reduces running costs, improving profitability.
- Competitive differentiation – increasingly demanded by the market – tenants, customers, guests, etc.
- Helps improve a company’s ESG credentials, with mandatory GHG emission reporting becoming more and more the norm, and will reduce a company’s risk exposure to inevitable government top-down responses to climate change.
UNDERSTANDING THE BUILDING LIFECYCLE AND CARBON EMISSIONS
A building’s carbon footprint must include emissions over its entire life cycle, from raw material extraction to demolition and waste disposal. This life cycle can be categorised into 4 distinct stages:
- Product Stage: related to material extraction, manufacturing, transportation, and assembly of building components. Steel and concrete, especially, are major carbon emitters.
- Construction Stage: From site preparation and construction activities to site waste management.
- Use Stage: This is where most attention usually falls, focusing on energy consumption for heating, cooling, lighting, and equipment operation.
- End-of-Life Stage: Demolition, waste disposal, and potential material reuse or recycling all need to be considered in a building’s carbon footprint.
Emissions from all these stages must be considered in GHG reporting. The emissions from each stage will fall into varying GHG emissions reporting scopes, (ie Scope 1, 2 or 3) depending on the company’s role, i.e., whether as an owner, developer, occupier, tenant, purchaser, seller, etc.
UNDERSTANDING THE CARBON FOOTPRINT –
Building related carbon emissions fall into two categories:
- Embodied Carbon: Emissions associated with material extraction, manufacturing, transportation, and the construction process.
- Operational Carbon: Emissions generated during the building’s use, i.e., from energy consumption for heating, cooling, lighting, and other functions.
EMBODIED VS. OPERATIONAL CARBON
Operational carbon is typically around 70% of a building’s total life cycle emissions and so currently receives the greatest attention. However, embodied carbon’s importance is expected to grow as new buildings become more energy efficient and their operational carbon reduces.
UNDERSTANDING THE TARGETS – CARBON NEUTRAL, CARBON ZERO, NET ZERO:
It is important to define which you are targeting.
Carbon Neutral means emissions are offset by carbon credits. This is achievable without any attempt to reduce emissions.
Net Zero means eliminating all emissions (or, practically speaking, at least 90-95%). There are 3 main Net Zero terms related to buildings:
- NZ Upfront Carbon: Targets emissions associated with building materials and construction processes (prior to the building use stage).
- NZ Energy: Targets annual emissions during the building use stage, through energy-efficient design and utilization of clean energy sources. This is normally the main area of focus.
- NZ Whole Life Carbon: Includes all emissions through the entire life cycle of the building. (i.e. zero embodied and zero operational carbon).
STRATEGIES FOR REDUCING THE CARBON FOOTPRINT OF NEW BUILDINGS:
Embodied Carbon Reduction Measures
- Minimize material use: Prioritize compact and efficient designs, explore modular construction methods that reduce waste, and avoid overdesign.
- Prioritise low-carbon materials: Utilize materials with recycled content, such as fly ash in concrete or reclaimed steel. Look for materials with Environmental Product Declarations (EPDs) that transparently disclose their environmental impact.
- Explore innovative alternatives: Consider bio-based materials like bamboo that lock carbon into the building. Investigate low-carbon cement alternatives, as they become available.
Operational Carbon Reduction Measures:
- Passive Design to Reduce Energy Demand:
- Optimize building orientation: Leverage natural daylight and shading to reduce reliance on artificial lighting and heating/cooling systems.
- Prioritize high-performance thermal insulation: Choose appropriate insulation materials for walls, roofs, and windows to minimize heat transfer.
- Maximize natural ventilation: Design for cross-ventilation and employ strategies like high ceilings and ceiling fans to reduce dependence on mechanical ventilation.
- Integrate biophilic design: Utilize green roofs, living walls, and landscaping to improve building performance and reduce urban heat island effects.
- Active Design – Smart Technologies and Efficient Systems:
- Invest in energy-efficient equipment: Choose high-efficiency HVAC systems, LED lighting, and water-saving plumbing fixtures.
- Implement smart controls: Employ sensors and intelligent systems to optimize energy use based on occupancy, daylight availability, and other factors.
- Consider on-site renewable energy generation: Explore options like solar panels, wind turbines, or geothermal systems to meet some of the building’s energy needs.
- Promote sustainable occupant behaviour: Encourage responsible energy consumption and waste reduction practices.
INTEGRATE CARBON EMISSION REDUCTION EARLY INTO THE DESIGN STAGE
To achieve emission reductions in new buildings it is essential to start early in the design stage and for the design team to be fully aligned in trying to achieve the goals.
It helps if the following studies are carried out early, to help establish these goals and the measures to adopt to achieve them:
- Life Cycle Analysis (LCA) studies, to evaluate the project’s embodied carbon, but also to evaluate other environmental impacts of the building.
- Building energy modelling (BEM) studies, to evaluate the expected energy consumption of the building, broken down by end users.
These studies enable the design to be benchmarked against other buildings, to identify hot spots in the design, and to evaluate the potential savings of proposed reduction measures.
Carrying out these analyses early in the design process allows for informed decision-making and for setting clear carbon reduction targets. These studies can then be repeated as the design progresses, to verify the design is still on track to achieve the emissions targets.
TRANSFORMING EXISTING BUILDINGS:
While constructing new low carbon buildings is crucial, addressing the vast existing building stock is equally important. Here are some key strategies:
- Conduct energy audits: Identify inefficient areas and potential energy-saving measures through comprehensive audits.
- Retrofit with energy-efficient equipment: Upgrade outdated systems with high-efficiency alternatives like LED lighting, variable-speed drives for motors, and efficient HVAC units. Retro commission the MEP systems, so they function efficiently.
- Implement smart controls: Install occupancy sensors, daylight sensors, and building management systems to optimize energy use.
- Address thermal envelope issues: Seal air leaks and improve insulation to minimize heat loss or gain.
- Explore renewable energy retrofits: Consider installing solar panels on suitable rooftops or integrating other on-site renewable energy sources.
NAVIGATING THE GREEN BUILDING CERTIFICATION LANDSCAPE:
Several green building certification schemes can guide efforts towards sustainability. However, it is important to understand their limitations regarding NZ:
- Many existing schemes primarily focus on operational carbon, with limited consideration for embodied carbon.
- Zero carbon certifications are often carbon neutral certifications, i.e. they rely on offsets, or on the purchase of off site 3rd party generated clean power, rather than on promoting low carbon design, construction and operation.
The situation with certification is changing continually, as certification bodies update themselves to match current trends, so please check with us which schemes may be beneficial to pursue.
THE ROAD TO NET ZERO: ADDRESSING KEY CHALLENGES:
While improvements are always possible, reducing embodied and operational carbon emissions by building design and operational improvements alone is unlikely to be sufficient. Achieving widespread NZ buildings requires tackling two key challenges:
- Emissions from the cement industry.
- Availability of clean energy.
EMISSIONS FROM THE CEMENT INDUSTRY
If cement was a country, it would be the 3rd largest CO2 emitter (after USA & China). 1 kg cement produces roughly 1kg CO2eq and 150,000kg are used globally per second.
Over 50% of cement’s emissions comes from the CO2 byproduct of the chemical reaction required to make cement. Much of the rest comes from the fossil fuels needed to generate the high heat to fuel this process. There are big challenges in decarbonising the cement industry:
- Currently few real alternatives to cement.
- Capturing the byproduct CO2 at local cement production sites is difficult.
- Generating the high temperatures required to make cement by electrical clean energy is difficult.
However, some possible pathways to reduce emissions exist:
In the short term
- Material substitution – use supplementary cementitious materials such as fly ash or pozzolans, use recycled materials, alternative binding materials, etc.
- Process efficiency improvements.
In the mid to longer term
- Substitute fossil fuels with green hydrogen or biofuels.
- Carbon capture, storage and utilisation.
CLEAN ENERGY
Transitioning to a national low-carbon energy grid is essential. Currently Thailand is lagging in this. Thailand’s solar generating capacity between 2017 and 2022 has been stuck at about 2.6% of total capacity.
BUILDING A GREENER FUTURE, TOGETHER
At Meinhardt, we believe embracing innovative design, efficient technologies, and collaborative partnerships can help achieve more sustainable buildings. Please contact us to discuss your low carbon building project and explore how we can help you achieve your sustainability goals.
John Mugford
Associate Director